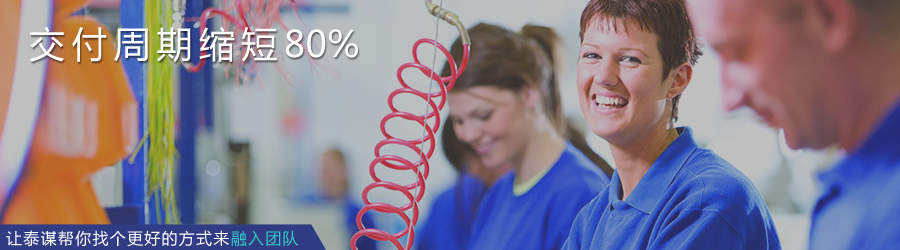
在定制化建筑材料公司实施精益降低75%的缺陷率
客户:领先的建筑材料制造商
地点:澳大利亚
挑战
我们的客户是亚太地区领先的高品质建筑材料制造商。客户邀请TXM帮助改善其元部件工厂。这家工厂比较复杂,过往业绩不佳,工厂的交付时间过长,成本较高而且返工率很高,这都阻碍了其业务的发展。
TXM的响应
TXM运用MAP中的价值流图绘制了端到端的流程图。它可以帮助识别造成长交付周期和高成本的根本原因。关键问题是在检查、纠错和返工过程中有很多缺陷产品,而且花费了大量的检验时间。TXM建立了Andon系统,使得员工可以暴露流程中的问题,确保问题可以快速解决,而不是将有缺陷的产品移交到下一工序。TXM引入了结构化的问题解决 – 基于TXM的“每日问题解决(SPED)”方法论。
TXM在全工厂实施了“每日精益领导力流程(LDLP)”,包括实践5S可视化管理、标准化作业和价值流图分析(MAP)。通过使用T卡显示需要完成的任务,并且每周进行审核,全工厂(包括便利设施)建立起了实践5S可视化标准体系。
标准化作业的实施包括:
- 建立TWI(技术作业指导书)、标准工作、领导标准工作来稳定和控制日常生产;
- 结合P5S的“清洁、紧固、润滑”任务和严格的每日问题解决SPED,建立TPM日常管理,重点关注那些指标不佳的机器。
更重要的是,我们的客户非常支持,任命了精益倡导者,实施了关键的结构性变化以支持改善的实施。
结果
在12个月的时间里,TXM实现了运营文化的根本改变,业绩得以显著地改善:
- 损失工时事故率降低了90%;
- 木制品交货周期降低了一半;
- 生产线缺陷减少了75%;
- 自动搁架生产过程的OEE提高了100%。
更重要的是,运营业绩已经明显地得到改善,客户更有信心继续在该工厂进行投资。