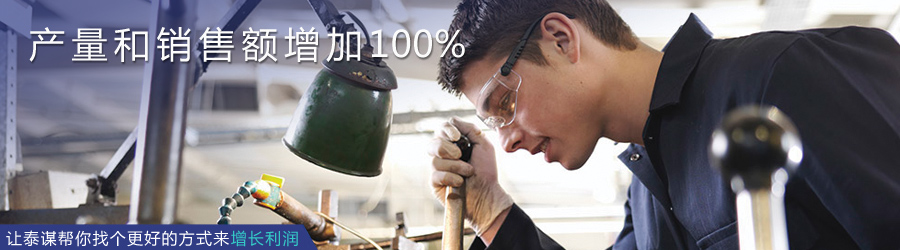
改善质量的五大精益技术
点击数:2,640 次
精益转型从30年前从戴明等人发起的“质量运动”开始。承载着客户对质量的期望,我们对于质量的认识在那段时间得到巨大的提高。TXM仍然发现一些公司,尤其是亚洲公司,对首次作对,还是存在着很大的困难。那么有哪些有用的技术和战略可以提高产品和服务的质量呢?
1:认真对待“质量第一”
我们都会说“质量第一”,但我们是认真的吗?我们都会停止生产而避免产生更多的不良品吗?我们都能很自信传达到客户手中的产品符合他们的要求吗?首次质量或者源头质量的概念的是非常简单的。也就是,每个流程都应为自己负责,且不会向下一个流程或者向客户传递缺陷。能达到这个更加困难。根据我的经验,普遍原因是经理发出模糊的信息。当产品需要修整、返工或者从客户手中退回时,他们会感到受挫,然后指责操作工,将过错归在他们身上。当压力变成达到销售业绩或生产目标,或者生产滞后,他们会给操作工压力,在没有很好设置的机器上工作。告诉他们“抓紧生产,回头我们会修理 设备”,或者当质量不符合规格时,批准“让步接受”,操作工和小组很容易发现这种假设,并认为这是很明确的传达“管理层都不严格要求质量,我们为什么要呢?”并且他们可能是对的。只有当你作为经理,100%坚持,准备停止流程,达到质量要求,你的团队才能看到你真的在认真对待,并且会跟随你的领导。
2.挑战100%的检查
如果我们对于向客户保证提供产品的质量,那么我们一定会检查100%的产品吧?错了!如果我们真的认真把关质量,我们就会竭尽所能在最初就阻止缺陷的产生。当流程失控(不能达到规格要求的质量),我们就需要检查产品,防止次品到达客户手中。有时候检查是强制的(比如航空和制药),或者不良反应比较严重所以需要检查(比如医用植入)。但检查应该是作为绝对的最后一道防御线,在正常条件下,是找不出缺陷的(因为它们在流程上游就被清除了)。但不幸的是我们经常看到(尤其在亚洲)100%检查被视为达到质量要求的方法。这行不通有几种原因。第一没有检察员或者检查系统是简单的,当有了缺陷,尽管你检查过了,你也知道一些将要传到客户那里。第二,检查仅仅作为“安全罩”,经常遮盖维修或换型不到位,操作员训练不足,或者流程走捷径。流程上游的人会觉得他们可以“不管不顾”,因为检察员在产品到达客户之前,会发现问题的。第三,检查花费是很大的。包括检查员的工资,不良品的生产,浪费的产量(首先生产了,再因不良品返工),在工厂移动和储存不两旁,以及延迟交货的花费,你会很快发现相对较少的不良品却占了生产成本的很大一部分。因此,检查的目的(如果你具备了)是找到和发现缺陷的源头。
引用下25年前我的导师的话:
- 检查不能脱离记录
- 记录不能脱离分析
- 分析不能脱离行动
3: 每日问题解决

使用问题条解决采用TXM“每日问题解决”方法,是Laminex 公司OEE提高和质量提高的重要因素
使用问题条解决采用TXM“每日问题解决”方法,是Laminex 公司OEE提高和质量提高的重要因素。
我们都讨厌出现问题。都希望事情进展顺利。然而生产中的进展顺利通常表示我们并没有每日观察影响团队达到质量目标能力的问题。教导TXM团队成员的日本精益教练说:“没问题就是有问题”。没问题意味着我们没有挑战当前的标准和试着提高。我对于检查中隐藏问题的意见是不错的例子。但发生错误时,我们需要抓住实际找出根本原因并消除它。我们认为解决问题应该是你公司每个团队日常车间会议的一部分,并且每个人都需要训练,使用或者参与简单的问题解决方法,如“5个为什么”和“鱼骨图”。我们推荐简单的磁性问题条,解决每日问题,至于更复杂的问题,建议使用A3问题解决方法或者8D。使用复杂的数据工作比如,实验设计和差异性分析的部分是很少用到的,因为大多数问题可以通过简单的工具解决,并且每个人都能理解。想要学习更多TXM解决每日问题,请访问我们的页面 精益问题解决,读读关于问题解决的博客。
4. 标准化工作
“如果你没有一个标准,那你怎么改善?” 标准化工作是精益生产系统的最基本因素。精益的第一条准则是“所有工作的用时、内容、结果和产出都是标准的。”这意味着每个人采取同样的方法,以同样的顺序,做同样的工作,在同一时间得到相同的结果。标准化工作指的不是绘制标准的操作流程,它是关于团队的员工讨论工作如何做,分解步骤,并在最佳办法上达成一致。然后这就成了标准,每个人都应该遵守这个标准,除非团队找到了更佳的办法。听起来很简单,符合逻辑,但当你每次以同样的方式,以同样的方法培训操作工做同样的事情,那么你应该得到相同的结果。这就是它怎么运行的。当出现错误时,第一个要问的问题就是“标准是什么?”,然后是“我们遵循了吗?”然后我们能很快的看到问题是否因背离标准(通过这个例子我们需要找出为什么)或者其它原因(比如物料质量缺陷)。标准化工作不仅仅局限于生产任务,也同时适用于公司的每一项活动。
5. 安灯
详见 安灯-精益的明灯
安灯系统是简单的信号指示系统,操作工用来快速发出指示,表示他/她有困难。操作工拉动绳索或者按下按钮,触发可视或者可听到的警报。小组长需要快速做出回应,帮助解决问题。如果小组长解决不了问题,问题将会升级,同时生产也将停止。这同样是一个简单但非同凡响的工具。它使得操作工树立了不能将质量不过关的问题流到下一个流程的意识,并使他们在出现问题的时候能停止生产线,敲响警报。这重新快速调整了公司的优先权,注重领导阶层支持操作工达到质量要求。这充满挑战,但一旦实行,就会带来巨大的变化。我们的精益资深顾问,托尼-麦克诺顿,当丰田接收在澳洲的原通用工厂,在任何其它资本投入之前,安灯系统是他们首先安装的东西。