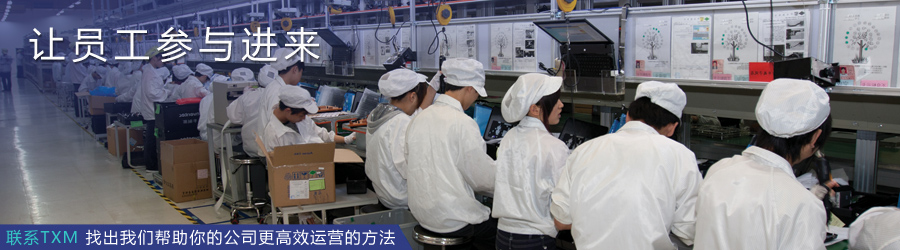
Sykes赛艇 – 一个奥运成功故事
点击数:3,235 次早在2008全球金融危机之前,世界领先的划艇制造商,Sykes分散在Geelong周边几个小工厂里。Sykes赛艇从多年以前就从木材转向先进的碳纤维复合材料,但制造业思维定势大致维持不变。传统的“工艺”的做法是用一个人从开始到完成做船,几乎所有的船需要最熟练的工匠做最后的检验,把船从上到下仔细查看,并做各种形式的返工。这种做法的结果是高度可变的输出和难以控制的库存积压。在项目开始时Sykes积压了6个月的库存,并面临未来中国进口船的压力。
Sykes董事长总经理Jeff Lawrence向Geelong制造局的企业业务顾问做了一次评估,评估这表明需要引进精益生产。
TXM指导Sykes团队开发价值流图。当Skkes对细长划艇应用TXM工厂布局后,就真正上路了。结果是一个“S”形流动布局,使企业可以达到潜在的两倍产量,但建立在从“一人做船”到“单件流”和标准工作。布局还涉及划艇按次序以每天几艘船的速度一步一步通过制造过程。在层压和塑形的工序间建立了一个小型的先进先出通道,但除了每天都需要移动以保持流动的船只。
Sykes赛艇对每一个流程步骤都做了标准工作分析,以平衡在每个工作站的工作量。这是复杂的,因为每艘艇都是不同的,而标准的工作得接受这个事实。随后Sykes采用了TXM团队称为“模糊标准”的工作,工作要素以几分钟为单位,必须允许周期时间在各个工作有一些变化。 船上的桨的装配件还增加了复杂性,这些装配件是在船制造的同时,经过一个完全不同的的流程。装配件延迟是积压船只的一个常见的原因。Sykes在他们的金工车间开发了改进流程,以确保装配件在船收尾工作之前交付在手。
除了确保流动,标准的工作过程产生了显著的生产力优势,完成任务的时间差异突显出来了,所有操作工都遵循最佳方法。经过一些初步的磨合,这种标准化方法已经为Sykes已经很高的质量标准作了进一步改善。
一旦标准的工作正在进行,最后阶段将重点转移到加强精益基础,5S,结构性问题解决和精益日常管理,班组长通过每天简短的“站立”会议指导他们的团队。这确保Sykes有稳定并不断提高的流程。
结果已经蔚为壮观。除了有一个一尘不染的工厂,现在还带来了一个提高的生产率和质量的世界,Sykes已减少他们的订单积压,从6个月至6个星期,随着产量增加,还提高生产率和减少返工。