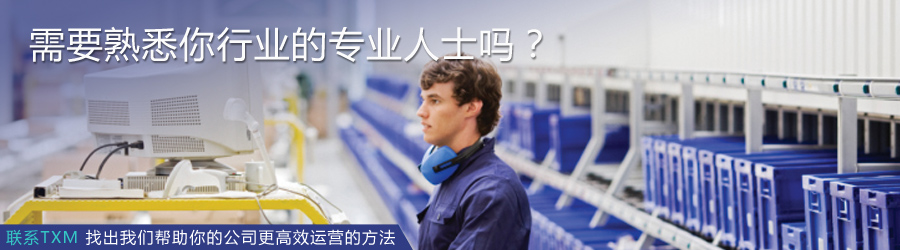
通过均衡化生产管理工厂工作负荷避免加急订单
点击数:2,600 次我们看到很多在生产和办公流程出现的一个问题,特别是在生产过程中造成的工作积压。这导致交付周期延长,变成急需处理的工作,而被提到工作计划前面。但许多读者都知道,因一项工作需要提到生产计划前面会导致其它工作的延迟,加快生产并不能起到很好的效果。最终,他们需要加速生产,并且很快会发现已经忘记原先的生产计划,因为每一样工作都已经提前了,计划一直都在变化。一些公司甚至将工作分为“一般紧急”和“非常紧迫”!这一切加速生产通常会导致生产周期缩短,计划反复修改,导致错误的生产顺序,以及其它诸多导致减产的问题,使得问题更加严重。
控制先入先出(FIFO)的生产流程

先入先出的方法有效控制各个生产流程
TXM,我们经常提倡的FIFO作为来控制工作顺序和确保原先交货时间的一种方法。然而,这只是答案的一部分。
如果FIFO流程不堪重负,会发生什么?一种方案是前面的流程需要停下来让后面的流程能够跟上。但是,一个更好的解决办法可能是在最开始就制止这种情况发生。
根据节拍时间均衡化生产
关键是要均衡生产。这是一个根本性的精益原则。一般要达到这个我们计算节拍时间,这是在客户购买我们的产品的平均频率。因此,举例来说,如果我们正在运行一个班次,包括休息时间,我们将每天工作约7个小时,或是420分钟。如果我们的每日平均销售额为210辆车,我们的生产节拍是由420除以210,2分钟。这意味着,我们需要每2分钟生产一辆车。在生产过程中的每一步,都要符合2分钟的生产节拍时间。但是,如果你不生产汽车呢?如果你每天甚至每个小时都在换型呢?许多生产商,比如定制机械设备类制造商,包装制造商以及其它许多产业,在这种情况下,我们需要其他的方式来衡量均衡化生产(见我们衡量流程型行业的文章),但总体原则不变 – 我们均衡化生产,以满足客户的需求。具体而言,这意味着我们将每个小时充分变成相应的效益,八个小时也就能得到八个小时的充分效益。

均衡化生产柜用来均衡订单到生产的流动
这可以延伸到你的生产计划。通过实现八小时工作时间的价值,你需要确保生产流程没有过载。这意味着当你拥有更大的生产力,你的机器和关键的生产单元只能依据客户的要求量而运转。
当你的客户的需求量开始达到最大生产能力时,该怎么办呢?
当你接近最大生产能力时,你可以回到当时能勉强满足客户需求量的时候。这样的念头会带来更多的工作。在这时你应该明白这过程中瓶颈在哪里。这通常可以原来按顺序排列的工作提前到生产计划前来发现。
在许多流程,生产的第一步骤是快速和产能大的,而后续的生产过程通常比较慢。这就诱导你使上游生产处于高负荷运作,诱惑则是“完全加载”上游的过程,“超前”和“保持机器一直忙”。但这一切会使得后续的生产瓶颈有了更多的积压。
因此,在确定你的瓶颈后,需要限制每天的生产量到最大生产限度,即使这意味着上游生产和机器未充分使用中。如果你发现你不能满足客户的需求,已经到达了极限,你需要增加工作时间或者增加人员和机器以此来扩大生产能力。无论如何你需要确保你每天的工作不超过瓶颈阶段的可用量。记住,使工厂排满工作并不意味着你能获得更多成品,事实上,加快生产可能使你的产量减少。
如何计划定拍工序?
在精益生产系统,我们的目标是只在一点上计划生产。然后,我们依据单件流生产或者先进先出生产。在订单生产过程中,起先生产的步骤生产订单,通常是在生产过程的开始作为定拍工序。这是我们决定要做什么东西的一个点,然后生产从这里开始。然而,这起步过程并不总是像瓶颈的过程。因此,当我们接近满负荷,我们需要确保,在定拍工序中释放出我们的工作不会超过下游生产的产能。
如果瓶颈变化了呢?

工厂里的纸盒像山一样堆积,这是由于生产紊乱造成的
对于某些流程中,我们已经注意到,生产瓶颈的过程可以通过产品结构改变。例如金属加工过程,瓶颈可能是在一天焊接,隔天在折弯加工,根据正在处理的工作组合。在这种情况下,最好的办法就是“均衡组合”。这是故意地排列生产序列,这样你就不需要全部堆到一起焊接或者一起折弯加工,这是我们为什么需要确保向客户说明的交付周期比我们自己的实际流程时间要长的原因。如果不可能均匀组合,那么你需要考虑各个工序的工作量需要消耗多少。如果“均衡组合”做不到,那么你将需要考虑所有工序的工作量决定释放多少。这种情况下,原先花八个小时产生的价值可能就不止需要这么点时间了,但它每天都会变化。如果平均是需要八个小时,你一周每天要花12个小时焊接,一周结束你会发现你有20个小时的工件在等待焊接。
总结
加快生产是由生产过程中过多的积压造成的。它是由于不均衡的过多的投入到生产中造成的,释放不均匀和过量生产造成。根据客户需求量均衡化生产能确保瓶颈和交付周期最小化,并使工作流程顺利。当你到达到能力极限,你需要考虑瓶颈并限制一天之内可以处理的数量。