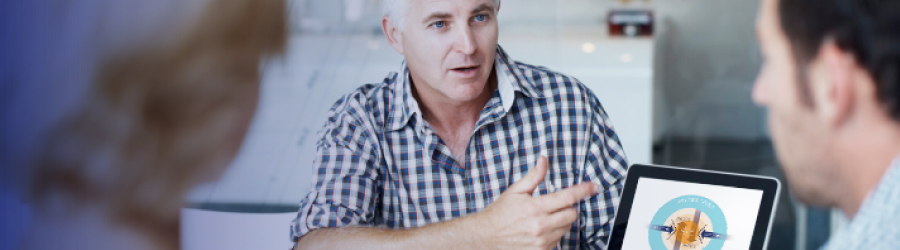
如何构建精益体系之实施篇(三)
点击数:2,818 次即使已经具备基础并制定了明确合理的目标,精益体系构建的实施依然是一个漫长复杂的过程,不同的企业会有不同的方式和路径,但是我们同样可以从那些最成功企业的历程中总结出一些具有通用性的实施方法和原则。
构建精益运营体系的第一步是建立相关的组织,组织中最关键的角色是领导和实施推动者,领导决定行动的目的和方向,为所有的行动提供支援和支持并确认行动的成果;而实施推动者扮演着技术专家的角色,他们在精益运营领域具有开阔的视野和丰富的经验,知道如何通过具体的系统方法在特定的范围内实施精益并取得成功。在丰田,这二个角色合二为一,领导即是该领域的专家,这不仅仅保证了策略执行的有效性和合理性,同时在人才培养方面也具有得天独厚的优势,因为上下级的每一次沟通和交流即是一次非常有针对性地培训。 客观事实是绝大多数的公司都不具备丰田领导者的精益技术优势,所以这些真正想构建精益运营体系的公司会另辟蹊径通过其他手段获得这种专业资源。或通过找寻专业的咨询公司来提供该种服务,或招聘精益专家在公司内任职,担任推动者的角色。丹纳赫的精益运营系统在建立初期借助了国际上专业的精益咨询机构的协助,而德尔福选择了另一种路,从外部聘请了二个精益专家在集团内担任要职并构建出德尔福的精益运营体系。根据李淑华总经理的介绍,这二位一手缔造德尔福体系的精益专家,一位专走上层路线,通过各种手段对德尔福的高层领导实施影响并从战略层面构建系统。另一位则擅长在生产现场实施现场改善指导以构建样板和标杆。正是这二位专家的通力合作,在产生从上往下对精益的关注和支持的同时又缔造了基于现场的最佳实践案例,最终推动德尔福精益体系的成型。
建立组织后,最关键的任务是建立标杆工厂和建立精益实施体系的标准化。标杆工厂的建立即集合相关优势资源按照精益原则改善选定工厂的生产运营体系使其达到较高的管理水平。标杆工厂的建立有诸多作用,首先是把理论和概念转化为实践经验并通过样板的卓越绩效来宣传精益运营体系的有效性,给雇员信心。其次标准工厂的建立过程亦是整个组织人才育成的过程,在标杆工厂的建立过程中,在实践中磨练和成长的新的精益专家们,会如同星星之火一般,最终点燃整个集团的精益转型。
精益实施体系的标准化包含精益相关活动形式的标准化和精益工具应用的标准化,正是这二个层次的标准化推动了精益理念在整个组织中快速有效的传播。精益活动形式的标准化即企业中实施精益改进的标准化模式。在丰田,车间现场所有的改善活动分为三类,即提案(合理化建议),QC小组活动和TPS改善,它们是持续改善这一核心理念的在不同层级上的体现。而德尔福则从时间维度对精益活动进行了详细的定义,例如每周例行的精益研讨会,每年1-2次的指导研讨会和每半年一次的全年运营领袖工厂参观。而丹纳赫则通过3-5天的改善周活动在整个集团内推行精益系统。正是通过这些规则化的执行活动的反复强化,改善之魂在企业内生根发芽。
精益实施模式的确立只是实施方式的形式化和标准化,这种标准化的流程迫使我们按照成熟的路径思考和实施以保证活动的有效性。但是活动只是载体,真正起到作用的是嵌套其中的精益工具,例如3-5天的改善周,既可以关于5S,也可以针对标准化作业,TPM和快速换型也可以嵌套其中。标准化的精益活动形式如同成形的容器,公司按照自己的需要在其他嵌套进特定的精益工具去攻城拔寨,有的放矢。
按照标准形式实施的精益工具也具有逻辑层次和先后顺序,这也是精益工具标准化的另一部分内容。例如标准作业的实现,需要有5S的执行基础。丹纳赫系统的定义了从传统到精益的12步方法(5S—标准化—快速换型—减少变化—物料看板体系—精实转变—生产准备流程—全员生产管理—日常管理—战略部署—VSM—事务性过程改善),它非常清晰明确的表达了精益工具的顺序和关系,也为我们的实施指出了明确的路径。
建立标杆和标准化后即需要开始体系的实施扩展。德尔福的精益运营系统在整个集团内的展开工作成果惊人,从唯一的一家标杆工厂渗透到其在全球的180家工厂,德尔福仅仅用了1-2年的时间。其成功的关键正是遵循入上逻辑并抓住要点:标准化的模块文件可以让全球所有的雇员学习到统一的精益知识,标杆工厂的建立则汇集不同工厂雇员,他们在标杆工厂通过实践获得了第一手的经验和认知,回到自己工厂后,实施符合自己工厂具体要求的精益模块,由于参照固定模式的实施方法,他们能有效规避风险。正是按照这种方法,德尔福精益系统推广实施的速率和成功率都很惊人。
成功推广和普及精益运营系统后,企业面临的新的挑战是如何维持和持续改进,在这个时候,一套在整个集团内使用的精益运营系统评估体系起到了举足轻重的作用。这套体系使用审查表的方法对相关模块的绩效进行了量化的评估。数据的量化最终在整个集团内促成了精益运营体系的巩固和持续优化。不同工厂之间的比较可以甄别各自的优劣势,这会促成不同工厂的互相学习和取长补短。而同一家工厂在不同时间段的比较则可以展现这个工厂精益运营的发展趋势,让后继乏力的工厂产生改进的压力和动力。
丰田,德尔福以及丹纳赫构建精益运营体系的经历和逻辑固然具有其特殊性,但是整个过程中他们却体现出卓越企业的勇气智慧以及对尽善尽美的不懈追求。每个企业都有宏伟的梦想,而精益运营系统正是实现这梦想的绝好载体。唯一能弥补梦想和现实差距的方法就是践行精益,值得我们反思的是,我们从这些优异的企业身上到底学到了什么?!
BY 陈辉(Ray Chen)
注:未经同意,谢绝转载。