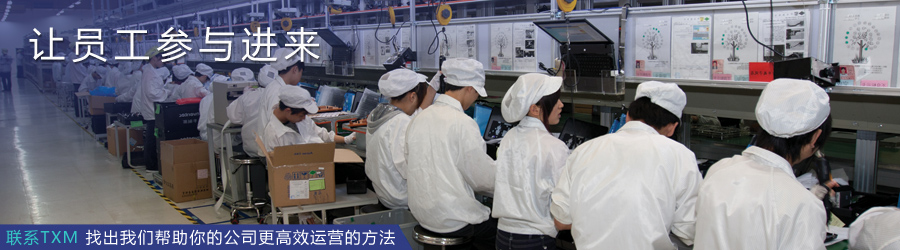
精益生产的五大原则
点击数:3,182 次精益生产是从生产的角度出发为了各种目标合理管理资源,而不是创造的价值到了客户手中变成了废物。原则上来讲,精益意味着消除生产流程中的低效:不必要的工作,生产不均,维护问题等。通过消除这些非增值流程,公司能更好地将资源用在增值流程中,花更多的时间在提高运营绩效上。
精益生产是由Henry Ford在生产部门实施的例子而广为人知。他将准时制生产实施到车辆生产中,着重通过尽可能消除库存,减少库存成本。现代精益生产理论源于丰田生产系统。丰田的理念在于消除三种类型的低效:非增值工作,工人超负荷工作,生产不均。在其它行业,精益理论可以运用于分辨资源浪费,通过清晰的方法实践,消除浪费。
五大精益生产原则
- 细化客户对于价值的期待和产品族的价值
- 辨别价值流的步骤,消除不能创造价值的浪费。
- 以紧凑的顺序,使增值步骤流线化,流向客户,或者下一个上游工序。
- 让客户拉动下一个上游工序。
- 重复系统的改进。
从哪里着手?
丰田成为最成功的精益制造商,但任何行业都可以从精益理念中受益。任何公司都能消除浪费,提高收益,比如工程师可以减小装配任务的复杂性;科学家可以减少测试上浪费的时间,会计能在月末报告中加快步伐,甚至是管理人员也可以提高管理和服从程序。
怎么开始?
从学习如何细化客户对于价值的期望 – 学习价值流程图。
在执行精益的时候,什么是最常见的错误?
将精益当做快速缩减成本的神奇办法。
从哪里开始?
与精益专家讨论,寻求帮助初步规划框架,这要根据你的实际情况和公司大小而定了。