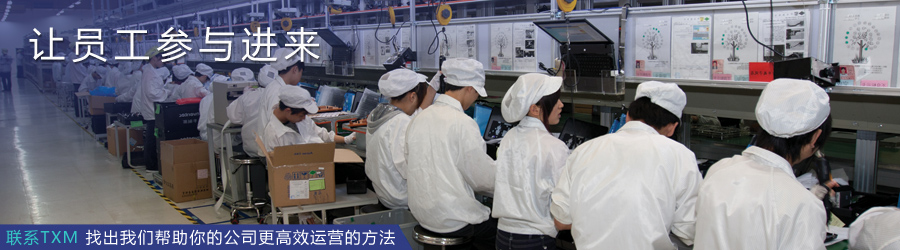
精益“培训”物有所值?
点击数:3,433 次精益“培训”物有所值?
手把手地在“现场”改善是团队学习精益的最佳方式
TXM在过去的7年中,访问了数百个在澳大利亚、中国和东南亚的生产基地。我们从制造商那里听到一个共同的故事是说:“我们在培训我们员工精益,但是我们没有看到任何结果”。
这种缺乏成功的后果是,许多企业已经完全放弃其精益项目。那么,问题出在那儿呢?
要明白为什么精益培训失败,你需要考虑哪些公司实施精益成功的。精益生产,丰田生产系统是一个管理系统,在一个成功的精干的组织水平。要取得成功需要改变,从顶部开始。光靠培训一线、中层员工不会带来什么改变,除非公司最高级领导人专注通过精益的改变。
培训失败的第一个原因是缺乏与公司战略和目标对齐。实施战略通常涉及互补性活动,旨在实现一个共同的目标一起工作的领导人和他的团队。学习和文化发生变化,但它是在重点领域实现战略。当战略目标得以实现,大家对精益的学习和信心增强,鼓励企业进一步扩展到整个企业。相比之下,“培训”往往基于预定设置的“能力”,这通常是由资格决定的,而不是公司战略的要求驱动的。训练后无法带来变化,无论是学员和他们的经理都失望和缺乏信心去再次尝试工具和技术。
第二个原因,不幸的是,培训质量。请廉价的咨询或培训公司,提供一个结构化的精益课程,是非常容易的事 。不幸的是,这些培训人员很少有指导学员通过在工作场所的实际变化的经验。这需要深刻理解精益思想和制造工艺和管理的能力,通过具有挑战性的变化,团队改善。因此许多与培训相关的“项目”是肤浅和缺乏真正影响的。
培训常常被看作是“成为精益” “最廉价”的选项,尤其是在澳大利亚,这样的课程是由政府资助的。培训师的成本不过是冰山一角。比方说,一个100人的精益培训。典型的精益课程可能会持续12个月,通常约4-8小时,每星期的学员参与。保守估计,工作人员的时间21000小时。在澳大利亚,一个平均劳动力成本,包括每小时30元,成本费用624,000美元。在亚洲,劳动力成本要低得多,但也考虑员工脱产完成培训,他们将有生产力损失。在今年年底,将有100人受培训,但不可能在工作场所发生任何变更,使用精益以解决生产力。根据我们的经验,在生产率提高20%,可在12个月,通过有重点的精益改善项目的经营策略(我们已经看到有改进高达50%的)驱动来实现。保守假设,开始6个月后的改善有效果,然后在首12个月可节省20,000小时或600,000美元。换言之,以“精益培训”的路子,将浪费这家公司共41,000小时或120万美元,失去了一年多的生产力, 即使他们的精益培训人员为是“免费”的。
那么,精益培训有一定的作用吗?我们的回答是肯定的,但只有在补充改善的过程,推动企业战略和旨在实现明确的可衡量的业务目标。我们建议使用精益的方法来解决你的公司关键问题,首先。这将导致直接的商业利益和构建精益方法的高级管理层的支持。聚焦精益培训,然后可以用来帮助发展关键的一线领导者,并给他们技能,以维持和建立初步改善。之后,从高级管理人员到一线大家公司各阶层联合,达到精益的成功有技能来维持进一步改善。你的企业可以期待实现你自己的可持续的精益生产系统这一难以实现的目标。