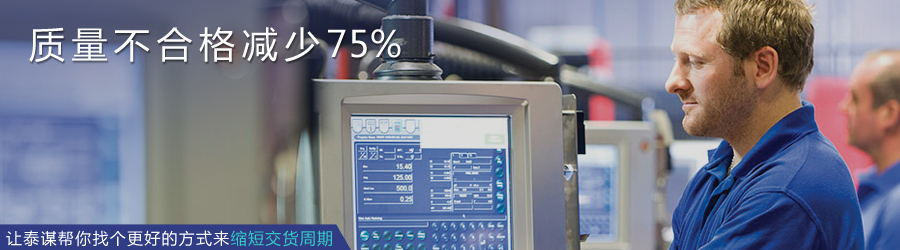
精益生产技巧 – 7大浪费
点击数:4,603 次在每个生产过程中,我们的目的是在客户需要购买的产品上增加价值。当给我们的产品增加价值的时候,我们需要通过一些任务来完成工作,但并不直接增值;举几个例子,比如换型和检查。在生产过程中其它的一些活动被认为是浪费。浪费指的是客户不愿意购买、毫无价值的部分。浪费是由价值而定义的,因此,我们首先要知道价值所在,才能知道其中的浪费。总之,浪费和客户的需要紧密相关。
我们怎样在生产系统中发现这些浪费呢?我们先通过价值流图,着手挖掘在流程中增值的步骤和周期时间。通过这个流程,我们知道了增值步骤需要的时间以及将部件传递到客户所需的整体交付周期。我们发现在两种时间总是存在很大差别。增值时间和交付周期的区别为我们在价值流中提供了减少隐藏的浪费的机会。以及在两种时间的差距中,我们能知道哪儿需要关注,发现浪费藏在哪儿。
七大浪费(MUDA型)是由丰田生产方式之父大野耐一定义的,以下就是7大浪费。
最初的七大浪费:
- 搬运(在流程运行中,移动不需要的产品)
- 库存(所有在制的零部件和没有得到处理的成品)
- 动作(操作工或者设备相对于流程运行所需,过多移动或者走动)
- 等待(等待下一步生产)
- 过量生产(比需求生产得更多)
- 过度加工(由于工具或者设计不良增加的活动)
- 缺陷(需要检查和处理缺陷的工作)
注意,现在已经增加了第八大浪费了,“未使用的人才”
什么是八大浪费呢?
- 缺陷–浪费的最简单形式就是零部件或者产品不符合标准。丰田质量成就就是由质量控制到质量保证的转化达到的-努力专注于流程的正确性,而不是检查结果。
- 过量生产-适时生产的关键因素,根据需求生产零部件或者产品。这是西方经济秩序提案的最大挑战, MRP在此提案上建立。这明确了订货费用,围绕换型次数以及需要将这些固定费用大量分摊下去的必要。丰田生产方式从较长的换型转变到单分钟换模。
- 等待-时间没被合理利用也算是浪费-我们承担薪水的支出,以及固定房租、汇率、照明和暖气设备等支出,因此我们应该有效地利用每分钟。丰田生产方式着重于机器和操作员没有充分得到利用,并着手解决。因此我们有新的预防性维护,创建生产流动和着重生产节拍。
- 运输-在区域间,楼层或者工厂内移动物品会在能源上产生费用-比如叉车消耗的汽油;一个运动带来其它花费。管理各个分散部件操作的工厂比在同一个生产单元的要难很多。
- 动作- 动作或走动从运输中分离出来。人在工厂和生产单元到处走动也是相当浪费的。机器操作员为了找一个工具或者螺丝,到处走动,不如我们将各种所需物品合理摆放在身边不远的地方,提高5S管理。
- 过度加工- 一个很好的例子就是关于零部件的表面加工要求的经验。原来的图纸需要旋转研磨器在车削后,提高表面加工。当数控机床安装后,所需的表面加工现能由新的机床设计的线路完成。因此研磨操作被取消。丰田生产方式的一条基本准则是只做需要做的事情。
- 库存- 现在大家都知道丰田生产方式的一个关键因素是适时生产系统来减少库存成本。通过减少库存,我们能在短交付周期下补充库存中发现问题。因此精益是持续改善的过程。
- 第八大浪费-未使用的人才-没有将员工的独特能力发挥到最佳水平。我们怎么能让每个人都参与到开发新的思想来获得改进和新产品呢?
为了让我们记住这些概念,首字母缩写是个有效的办法,下面有几个例子,
记住7大浪费的简单办法是 TIMWOOD:
T:运输
I:库存
M:动作
W:等待
O:过度加工
O:过量生产
D:缺陷
另一个简单的方式是 NOM TIME: 现在是时候消除浪费了:
N:质量不符合
O:过量生产
W:等待
T:运输
I:库存
M:动作
E:过度加工
8大浪费,我们用缩写字母DOWNTIME,这是十分有用的记忆法:
D:缺陷
O:过量生产
W:等待
N:未使用的人才
T:运输
I:库存
M:动作
E:过度加工